图书介绍
车用涡轮增压器结构可靠性【2025|PDF|Epub|mobi|kindle电子书版本百度云盘下载】
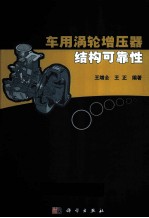
- 王增全,王正编著 著
- 出版社: 北京:科学出版社
- ISBN:9787030362827
- 出版时间:2013
- 标注页数:305页
- 文件大小:52MB
- 文件页数:315页
- 主题词:汽车-涡轮增压器-结构设计-研究
PDF下载
下载说明
车用涡轮增压器结构可靠性PDF格式电子书版下载
下载的文件为RAR压缩包。需要使用解压软件进行解压得到PDF格式图书。建议使用BT下载工具Free Download Manager进行下载,简称FDM(免费,没有广告,支持多平台)。本站资源全部打包为BT种子。所以需要使用专业的BT下载软件进行下载。如BitComet qBittorrent uTorrent等BT下载工具。迅雷目前由于本站不是热门资源。不推荐使用!后期资源热门了。安装了迅雷也可以迅雷进行下载!
(文件页数 要大于 标注页数,上中下等多册电子书除外)
注意:本站所有压缩包均有解压码: 点击下载压缩包解压工具
图书目录
第1章 概述1
1.1涡轮增压器的发展概况1
1.1.1涡轮增压器的原理与应用1
1.1.2涡轮增压器的基本结构形式3
1.1.3涡轮增压器的发展趋势10
1.2可靠性工程的发展概况15
1.3增压器结构可靠性研究的必要性17
1.4本书的主要内容21
第2章 可靠性基本理论与方法23
2.1可靠性基本概念及常用度量指标23
2.1.1可靠性的基本概念23
2.1.2可靠性的常用度量指标24
2.2应力-强度干涉模型及其拓展27
2.2.1应力-强度干涉模型27
2.2.2应力-强度干涉模型的拓展28
2.3零部件疲劳可靠度计算模型29
2.3.1确定性恒幅循环载荷作用下的零部件疲劳可靠度计算30
2.3.2不确定性恒幅循环载荷作用下的零件疲劳可靠度计算31
2.4具有多种失效模式的零部件可靠性模型33
2.4.1传统的多失效模式零部件可靠性模型34
2.4.2考虑共因失效的多失效模式零部件可靠性模型35
2.5系统可靠性模型36
2.5.1典型的系统可靠性模型37
2.5.2失效相关系统可靠性模型40
2.5.3系统等效强度及其概率分布44
2.6以载荷作用次数为寿命指标的时变可靠性模型48
2.6.1以载荷作用次数为寿命指标的零部件时变可靠性模型48
2.6.2以载荷作用次数为寿命指标的系统时变可靠性模型51
2.6.3以载荷作用次数为寿命指标的失效率计算模型53
2.7以时间为寿命指标的时变可靠性模型56
2.7.1以时间为寿命指标的零部件时变可靠性模型57
2.7.2以时间为寿命指标时的系统时变可靠性模型62
2.8基于时变可靠性的可靠寿命确定与失效期划分方法67
第3章 增压器涡轮结构可靠性69
3.1涡轮的工作状态参数分析69
3.2涡轮的载荷与应力分析77
3.2.1涡轮在离心载荷作用下的应力分析77
3.2.2涡轮在热载荷作用下的应力分析80
3.2.3涡轮在气动载荷作用下的应力分析90
3.2.4不同载荷对涡轮应力影响的对比92
3.2.5降低涡轮应力的措施96
3.3典型涡轮材料的力学性能99
3.4涡轮叶片振动分析102
3.4.1涡轮叶片振动分析的理论基础103
3.4.2涡轮叶片振动特性及其影响因素106
3.4.3涡轮叶片振动激励与共振线图111
3.4.4降低涡轮叶片振动的措施113
3.4.5涡轮振动参数的测试116
3.5涡轮超速破坏可靠性分析与评价120
3.5.1涡轮的超速破坏失效模式120
3.5.2基于传统安全系数法的涡轮超速破坏评价121
3.5.3涡轮超速破坏失效模式时变可靠性模型122
3.5.4实例123
3.6涡轮轮毂疲劳可靠性分析与寿命预测125
3.6.1涡轮轮毂部位的疲劳应力126
3.6.2涡轮轮毂的疲劳强度127
3.6.3涡轮轮毂疲劳可靠性模型128
3.6.4涡轮轮毂疲劳可靠性变化与可靠寿命确定129
3.7涡轮叶片振动可靠性分析与评价130
3.7.1涡轮叶片振动参数不确定性特征分析131
3.7.2涡轮叶片振动失效判据132
3.7.3涡轮叶片振动时变可靠性模型134
3.7.4涡轮叶片振动可靠性变化研究与可靠寿命确定135
第4章 涡轮增压器转子-轴承系统结构可靠性138
4.1涡轮增压器转子-轴承系统的结构特点138
4.1.1概述138
4.1.2涡轮增压器轴系结构布置形式139
4.1.3常见涡轮增压器转子-轴承系统的结构特点140
4.2涡轮增压器转子-轴承系统动力学理论基础142
4.2.1单自由度系统的振动方程142
4.2.2多自由度系统的振动方程146
4.2.3常用线性系统的稳定性判据148
4.2.4非线性振动系统简介152
4.2.5振动方程常用求解方法154
4.2.6转子-轴承系统动力学方程建立162
4.2.7浮环轴承润滑机理及动特性系数的计算167
4.3涡轮增压器的非线性振动176
4.4涡轮增压器转子-轴承系统动力学仿真分析178
4.4.1涡轮增压器转子-轴承系统的有限元模型178
4.4.2涡轮增压器转子-轴承系统的静态特性计算180
4.4.3涡轮增压器转子-轴承系统的线性动力学分析181
4.4.4涡轮增压器转子-轴承系统非线性动力学分析187
4.5涡轮增压器转子的动平衡192
4.5.1转子平衡的基本概念192
4.5.2刚性转子的动平衡等级193
4.5.3涡轮增压器转子动平衡量计算方法195
4.5.4涡轮增压器转子动平衡去重要求197
4.6涡轮增压器转子-轴承系统的密封与润滑199
4.6.1涡轮增压器转子-轴承系统常见密封结构199
4.6.2涡轮增压器转子-轴承系统的润滑形式203
第5章 压气机叶轮结构可靠性205
5.1压气机叶轮的工作状态参数分析205
5.2压气机叶轮的载荷与应力分析207
5.2.1压气机叶轮在离心载荷作用下的应力分析207
5.2.2压气机叶轮在热载荷作用下的应力分析211
5.2.3压气机叶轮在气动载荷作用下的应力分析217
5.2.4不同载荷对压气机叶轮应力影响的对比分析218
5.3压气机叶轮典型材料的力学性能221
5.3.1铸造成型压气机叶轮典型材料的力学性能221
5.3.2铣削成型压气机叶轮典型材料的力学性能223
5.4压气机叶轮振动分析226
5.4.1压气机叶轮的振动频率与振型226
5.4.2不同载荷对压气机叶轮振动特性的影响226
5.5压气机叶轮的超速破坏可靠性分析与评价230
5.5.1压气机叶轮超速破坏的应力与强度231
5.5.2压气机叶轮超速破坏时变可靠性模型233
5.5.3压气机叶轮超速破坏可靠度与失效率变化研究234
5.5.4压气机叶轮超速破坏可靠寿命的确定235
5.6压气机叶轮轮毂疲劳可靠性评价与寿命预测236
5.6.1压气机叶轮轮毂疲劳应力237
5.6.2压气机叶轮轮毂疲劳强度238
5.6.3压气机叶轮轮毂疲劳可靠性模型239
5.6.4压气机叶轮轮毂疲劳可靠寿命确定241
5.7压气机叶轮叶片振动可靠性分析与评价242
5.7.1压气机叶轮叶片振动参数不确定性特征分析242
5.7.2压气机叶轮叶片振动失效判据244
5.7.3压气机叶轮叶片振动时变可靠性模型246
5.7.4压气机叶轮叶片振动可靠性变化研究与可靠寿命确定247
第6章 涡轮增压器故障树与典型失效案例250
6.1典型车用涡轮增压器故障树分析250
6.1.1故障树分析的基本概念与建树方法250
6.1.2典型车用涡轮增压器的故障树254
6.2某型涡轮增压器旁通放气阀杆疲劳断裂研究257
6.2.1旁通放气阀杆断裂失效模式分析257
6.2.2旁通放气阀杆断裂失效机理258
6.2.3旁通放气阀失效原因及其改进措施260
6.2.4结论261
6.3增压器压气机叶片断裂故障分析262
6.3.1压气机叶轮的故障原因分析263
6.3.2压气机叶轮的改进设计264
6.3.3压气机气动性能试验验证265
6.3.4压气机叶轮可靠性试验验证267
6.4增压器涡轮叶片断裂故障分析268
6.4.1涡轮叶片断裂故障描述268
6.4.2涡轮叶片断裂故障原因分析269
6.4.3结论与改进建议271
6.5异物进入导致的压气机叶轮损坏故障分析271
6.5.1空气滤胶块脱落引起的压气机叶轮损坏271
6.5.2进气连通管焊渣脱落引起的压气机叶轮损坏272
6.6增压器隔热罩破损故障分析273
6.6.1增压器隔热罩破损现象273
6.6.2隔热罩破损故障原因分析274
6.6.3隔热罩破损故障机理分析275
6.6.4改进措施及试验验证277
第7章 涡轮增压器结构可靠性试验279
7.1涡轮增压器常用试验参数的测量279
7.1.1增压器转速的测量279
7.1.2压气机流量的测量281
7.1.3总温的测量282
7.1.4总压与静压的测量283
7.1.5振动参数的测量285
7.2涡轮增压器叶轮超速破坏试验287
7.2.1试验目的287
7.2.2试验条件287
7.2.3试验方法287
7.3涡轮增压器壳体包容试验290
7.3.1试验目的290
7.3.2试验条件290
7.3.3试验方法290
7.4涡轮增压器轴系振动试验292
7.4.1试验目的292
7.4.2试验条件292
7.4.3试验方法292
7.5涡轮增压器结构考核试验294
7.5.1试验目的294
7.5.2试验条件294
7.5.3试验方法295
参考文献298
附录 标准正态分布表304
热门推荐
- 3288910.html
- 2752609.html
- 3001789.html
- 3092358.html
- 514964.html
- 1198507.html
- 1768836.html
- 2763275.html
- 3280170.html
- 1259634.html
- http://www.ickdjs.cc/book_496919.html
- http://www.ickdjs.cc/book_3212090.html
- http://www.ickdjs.cc/book_2463583.html
- http://www.ickdjs.cc/book_181321.html
- http://www.ickdjs.cc/book_1427343.html
- http://www.ickdjs.cc/book_3191777.html
- http://www.ickdjs.cc/book_361738.html
- http://www.ickdjs.cc/book_527609.html
- http://www.ickdjs.cc/book_573669.html
- http://www.ickdjs.cc/book_1672013.html